Protect Dairy Products with Anti-Listeria Solution
Since 2017, dairy and fermented products have been associated with a quarter of Listeria contamination cases, underscoring the need for proactive protection. Inneo, our advanced anti-Listeria solution, protects your products, ensuring safety without compromise.
Whether before or after pasteurization, our exceptional natural solution is a powerful defence against Listeria, ensuring the safety of your products and maintaining client trust.
Inneo: Redefining dairy safety
Inneo takes dairy safety to the next level by providing an essential layer of protection whether before or after pasteurization. By spraying on or blending directly into your product mixture, it dramatically reduces the risk of Listeria contamination.
Thanks to its innovative antimicrobial formula, Inneo ensures uniform coverage, keeping your dairy products safe without compromising on quality. Plus, as a food processing aid, it won’t appear on labels—giving you the flexibility to meet the growing demand for clean-label and sustainable products.
DOWNLOAD THE BROCHURE
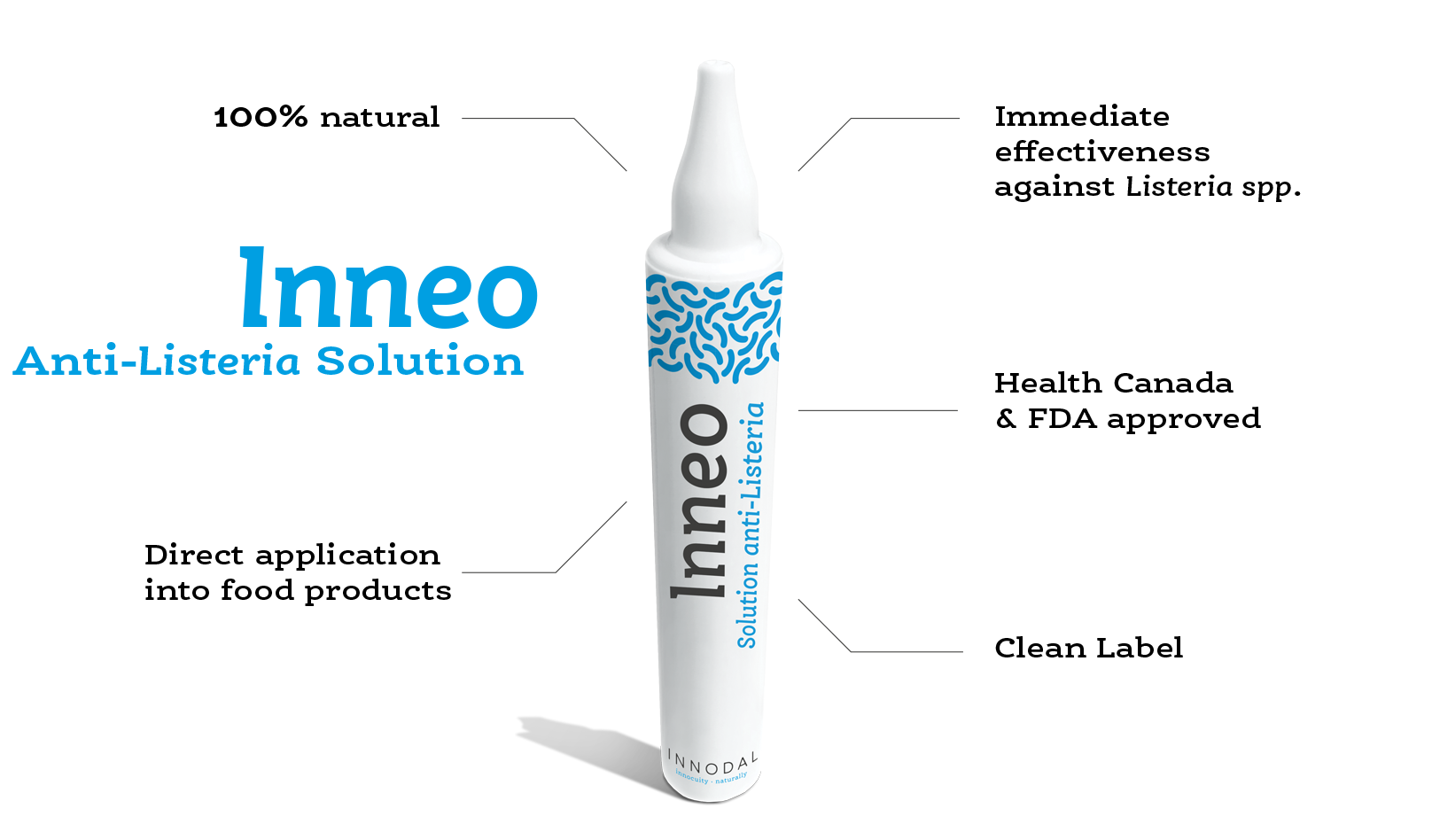
Inneo takes dairy safety to the next level by providing an essential layer of protection whether before or after pasteurization. By spraying on or blending directly into your product mixture, it dramatically reduces the risk of Listeria contamination.
Thanks to its innovative antimicrobial formula, Inneo ensures uniform coverage, keeping your dairy products safe without compromising on quality. Plus, as a food processing aid, it won’t appear on labels – giving you the flexibility to meet the growing demand for clean-label and sustainable products.
DOWNLOAD THE BROCHURE
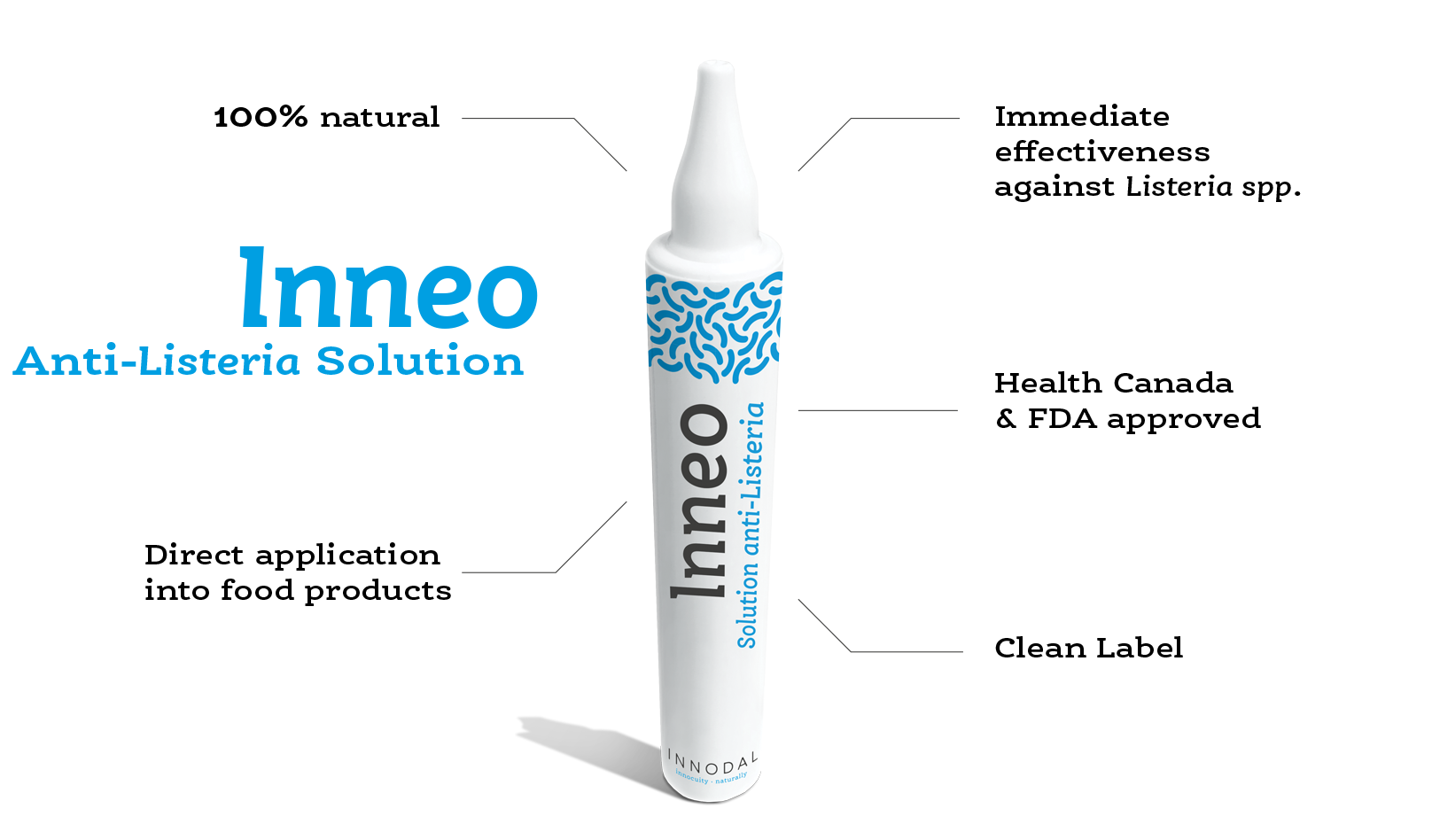
Inneo’s seamless integration into dairy production
Inneo is designed to easily integrate into your current dairy production process, guaranteeing that your products maintain their optimal quality. Tailored to meet even the stringent industry standards, this system delivers unmatched safety and consistency with every application thanks to its advanced dosing control.
Tailor the application to perfectly align with your specific requirements.
Inneo’s seamless integration into dairy production
Inneo is designed to easily integrate into your current dairy production process, guaranteeing that your products maintain their optimal quality. Tailored to meet even the stringent industry standards, this system delivers unmatched safety and consistency with every application thanks to its advanced dosing control.
Tailor the application to perfectly align with your specific requirements.

What sets Inneo apart?
Ensure consistent quality
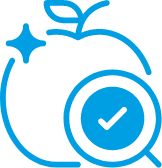
With Inneo, your dairy products maintain their original taste, smoothness, and visual appeal – ensuring complete client satisfaction.
Guard your reputation
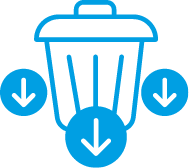
Inneo effectively mitigates the risks linked to Listeria, empowering you to safeguard your brand against costly recalls and preserving your profit margins.
Unlock global markets
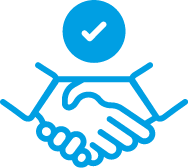
Inneo ensures your dairy products meet both local and international food safety standards, empowering you to confidently explore new market opportunities.
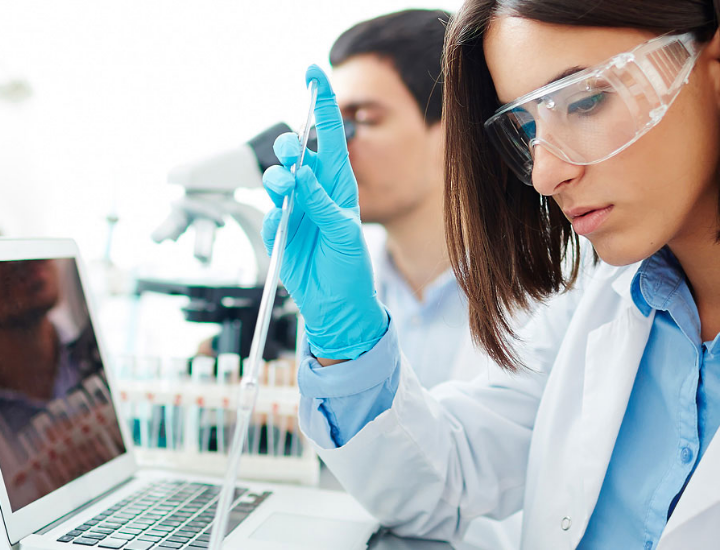
A team of experts at your service
Our team of specialists is committed to guiding you through the implementation and optimization of Inneo.
Step 1: Initial discovery, needs assessment, and on-site visit
We begin with a discovery meeting to assess your microbiological challenges, food safety objectives and operational workflows. Following this, we conduct an on-site visit to understand your current processes and determine the most effective way to use Inneo.
Step 2: Laboratory testing and validation
Compatibility tests are carried out in our ISO 17025 certified laboratory to ensure that there are no interactions between products. Depending on specific needs and regulatory requirements, we can also conduct additional testing, such as challenge studies and shelf-life evaluations.
Step 3: Comprehensive reporting and implementation
This step includes a detailed report summarizing test results, key insights, and actionable recommendations. It also features a customized implementation strategy and phased rollout plan designed to minimize operational disruptions.
Step 4: On-site support and application rollout
Our technical team provides hands-on assistance during the initial application phase, helping with system setup, real-time adjustments, and process optimization. Ongoing support is available for equipment calibration, validation, and troubleshooting.
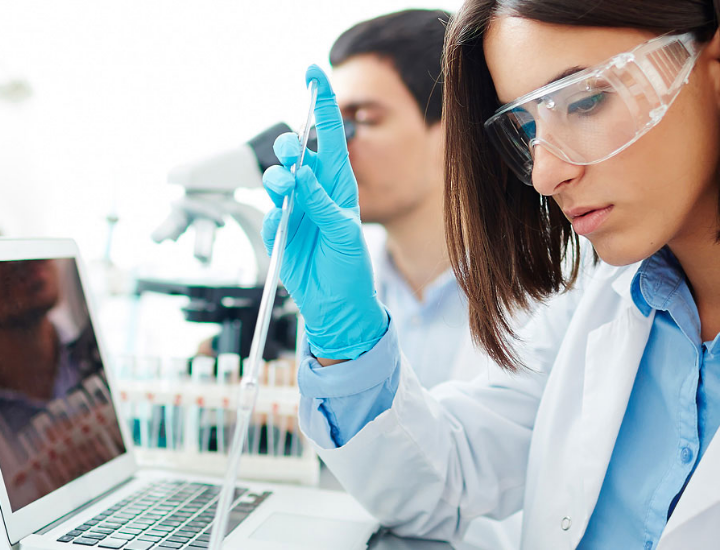
A team of experts at your service
Our team of specialists is committed to guiding you through the implementation and optimization of Inneo.
Step 1: Initial discovery, needs assessment, and on-site visit
We begin with discovery meetings to gain a clear understanding of your microbiological challenges, food safety objectives, and operational workflows. Following this, we conduct an on-site visit to evaluate your current production processes and identify any necessary modifications to ensure the seamless integration of our solution.
Step 2: Laboratory testing and validation
Compatibility tests are carried out in our ISO 17025 certified laboratory to ensure that there are no interactions between products. Depending on specific needs and regulatory requirements, we can also conduct additional testing, such as challenge studies and shelf-life evaluations.
Step 3: Comprehensive reporting and implementation
This step includes a detailed report summarizing test results, key insights, and actionable recommendations. It also features a customized implementation strategy and phased rollout plan designed to minimize operational disruptions.
Step 4: On-site support and application rollout
Our technical team provides hands-on assistance during the initial application phase, helping with system setup, real-time adjustments, and process optimization. Ongoing support is available for equipment calibration, validation, and troubleshooting.